In the production process, foundry companies will inevitably encounter casting defects such as shrinkage, bubbles, and segregation, resulting in low casting yields. Re-melting and production will also face a large amount of manpower and electricity consumption. How to reduce casting defects is a problem that foundry professionals have always been concerned about.
Regarding the issue of reducing casting defects, John Campbell, a professor from the University of Birmingham in the UK, has a unique understanding of reducing casting defects. As early as 2001, Li Dianzhong, a researcher at the Institute of Metal Research, Chinese Academy of Sciences, carried out hot processing process organization simulation and process design under the guidance of Professor John Campbell. Today, Intercontinental Media has compiled a list of the top ten principles for reducing casting defects proposed by international casting master John Campbell.
1.Good castings start with high-quality smelting
Once you start pouring castings, you must first prepare, check and handle the smelting process. If required, the lowest acceptable standard can be adopted. However, a better option is to prepare and adopt a smelting plan close to zero defects.
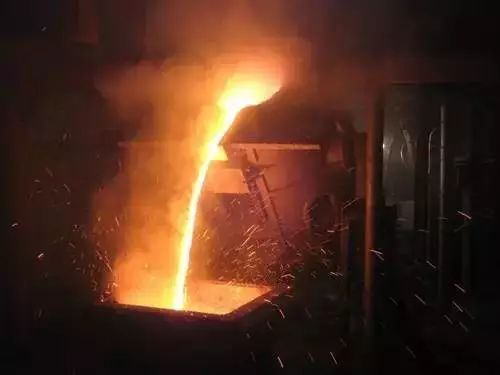
2.Avoid turbulent inclusions on the free liquid surface
This requires avoiding excessive flow velocity on the front free liquid surface (meniscus). For most metals, the maximum flow velocity is controlled at 0.5m/s. For closed casting systems or thin-walled parts, the maximum flow velocity will be appropriately increased. This requirement also means that the falling height of the molten metal cannot exceed the critical value of the "static drop" height.
3.Avoid laminar inclusions of surface condensate shells in the molten metal
This requires that during the entire filling process, no front end of the molten metal flow should stop flowing prematurely. The molten metal meniscus in the early stage of filling must remain movable and not be affected by the thickening of the surface condensate shells, which will become part of the casting. To achieve this effect, the front end of the molten metal can be designed to expand continuously. In practice, only the bottom pouring "uphill" can achieve a continuous rising process. (For example, in gravity casting, it starts to flow upward from the bottom of the straight runner). This means:
Bottom pouring system;
No "downhill" falling or sliding of the metal;
No large horizontal flows;
No front-end stoppage of the metal due to pouring or cascading flows.
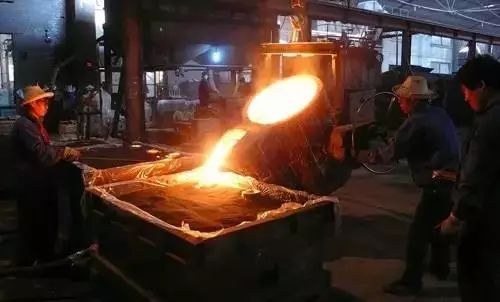
4.Avoid air entrapment (bubble generation)
Avoid air entrapment in the pouring system from causing bubbles to enter the cavity. This can be achieved by:
Reasonably designing the stepped pouring cup;
Reasonably designing the sprue for quick filling;
Reasonably using the "dam";
Avoid using the "well" or other open pouring system;
Using a small cross-section runner or using a ceramic filter near the connection between the sprue and the cross runner;
Using a degassing device;
The pouring process is uninterrupted.
5.Avoid sand core pores
Avoid air bubbles generated by the sand core or sand mold from entering the molten metal in the cavity. The sand core must have a very low air content, or use appropriate exhaust to prevent the generation of sand core pores. Clay-based sand cores or mold repair glue cannot be used unless they are completely dry.
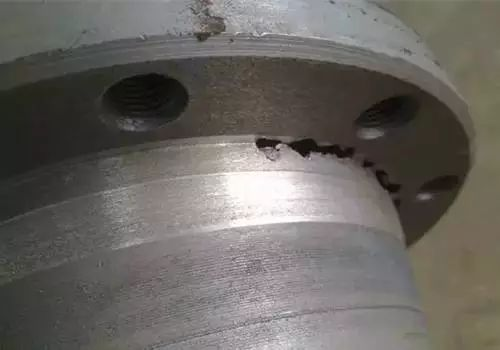
6.Avoid shrinkage cavities
Due to convection and unstable pressure gradients, it is impossible to achieve upward shrinkage feeding for thick and large cross-section castings. Therefore, all shrinkage feeding rules must be followed to ensure a good shrinkage feeding design, and computer simulation technology must be used for verification and actual casting samples. Control the flash level at the connection between the sand mold and the sand core; control the thickness of the casting coating (if any); control the alloy and casting temperature.
7.Avoid convection
Convection hazards are related to solidification time. Thin-walled and thick-walled castings are not affected by convection hazards. For medium-thickness castings: reduce convection hazards through casting structure or process;
Avoid upward shrinkage feeding;
Turning over after pouring.
8.Reduce segregation
Prevent segregation and control it within the standard range, or the composition limit area allowed by the customer. If possible, try to avoid channel segregation.
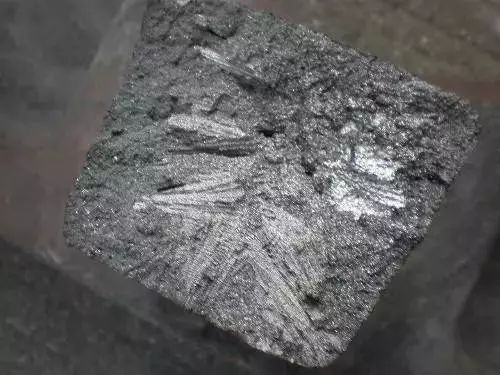
9.Reduce residual stress
After solution treatment of light alloys, do not quench with water (cold or hot water). If the stress of the casting does not seem to be large, use polymer quenching medium or forced air quenching.
10.Given reference points
All castings must be given positioning reference points for dimensional inspection and processing.
Post time: May-30-2024